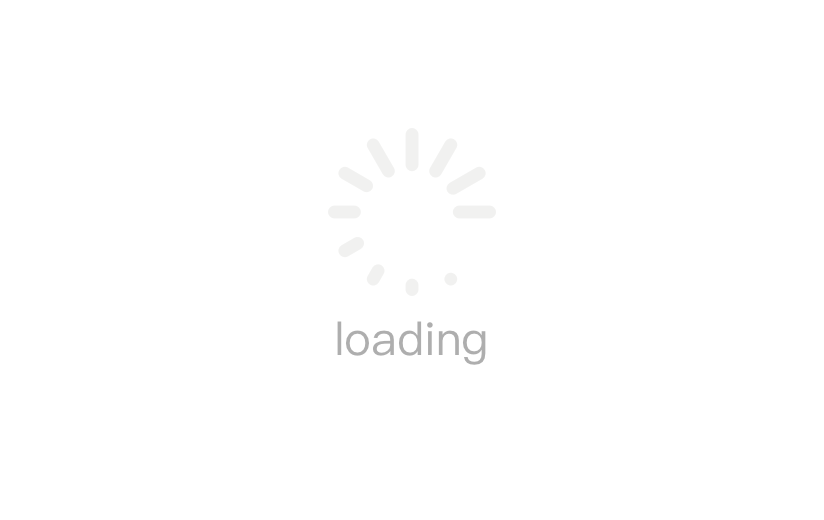
Sheet metal features light weight, excellent strength, excellent electrical conductivity, low cost, high performance and ease of massive production. Because of those outstanding features, sheet metal is widely used in electronics, communication, automobile, medical equipment, etc.. As sheet metal is having more and more applications, the design of sheet metal piece has become an important step in the development of the products. The mechanical engineers need to know the design requirement of the sheet metal pieces so that the sheet metal can fulfill the requirement of the product function and the appearance while at the same time making the diel easy and low cost.
Traditional sheet metal cutting device accounts for a big market share in the market. On one thing, they are less expensive. On the other hand, they have their own advantages. But when laser cutting technique is introduced to the market, all of their advantages become so “small”.
CNC shearing machineCNC shearing machine is often used for linear cutting. Although it can cut a 4-meter sheet metal with only one-time cutting, it is only applicable to sheet metal that requires linear cutting.
Punching machinePunching machine has greater flexibility on curved processing. One punching machine can have one or multiple square or round plunger chips and complete certain sheet metal pieces at one time. This is pretty common in cabinet industry. What they require most is linear cutting, square hole cutting, round hole cutting and so on and the patterns are relatively simple and constant. The advantage of punching machine is that it has fast cutting speed in simple pattern and thin sheet metal. And its disadvantage is that it has limited power in punching thick steel plates. Even it is capable of punching those plates, it still has the drawbacks of collapse on the work piece surface, long mould developing period, high cost and low flexibility. In the foreign countries, steel plates with more than 2mm thickness are often processed by more modern laser cutting machine instead of punching machine. That is because: 1. Punching machine leaves a bad quality surface on the work piece; 2. Punching thick steel plates requires higher capacity punching machine, which wastes lots of space; 3. Punching machine makes a big noise while working, which is not friendly to the environment.
Flame cuttingFlame cutting is the most traditional cutting. It used to take up big market share because it doesn’t cut too much and the flexibility to add other procedures. It is now often used to cut thick steel plates of more than 40mm thickness. However, it is often characterized by big thermal deformation, wide cutting edge, waste of materials, slow cutting speed, so it is only suitable for rough machining.
Plasma cuttingPlasma cutting, just like flame cutting, has big heat-affecting zone but with higher precision and efficiency. In the domestic market, the upper limit of cutting precision of top CNC plasma cutting machine has already reached the lower limit of the laser cutting machine. When cutting carbon steel plates of 22mm thickness, plasma cutting machine has already reached 2m/min speed with clear and smooth cutting surface. However, plasma cutting machine also has high degree of thermal deformation and big inclination and can not satisfy higher precision requirement. What’s more, its consumables are quite expensive.
High pressure waterjet cuttingHigh pressure waterjet cutting uses high speed water flow mixed with carborundum to cut the sheet metal. It has almost no limitation on the materials and its cutting thickness can reach almost 100+mm. It can also be used to cut easy-to-crack materials like ceramics, glass and copper and aluminum. However, waterjet cutting machine has pretty slow cutting speed and produces too much waste and consume too much water, which is not friendly to the environment.
Laser cutting
Laser cutting is an industrial revolution of sheet metal processing and is known as the “processing center” in sheet metal processing. Laser cutting has high degree of flexibility, high cutting efficiency and low product lead time. No matter whether it is simple or complicated parts, laser cutting machine can perform one-time high precision cutting with superior cutting quality. Many people think that in the coming 30 or 40 years, laser cutting technique will become the dominated cutting method in sheet metal processing.
While laser cutting machine is having a bright future, its accessories need to keep updated. As a reliable laser chiller manufacturer, S&A Teyu keeps upgrading its industrial water chillers to be more user-friendly and have more functions. After 19 years of development, the water chiller systems developed by S&A Teyu can satisfy almost every category of the laser sources, including fiber laser, YAG laser, CO2 laser, ultrafast laser, laser diode, etc.. Go check out your ideal industrial water chiller for your laser systems at https://www.teyuchiller.com/
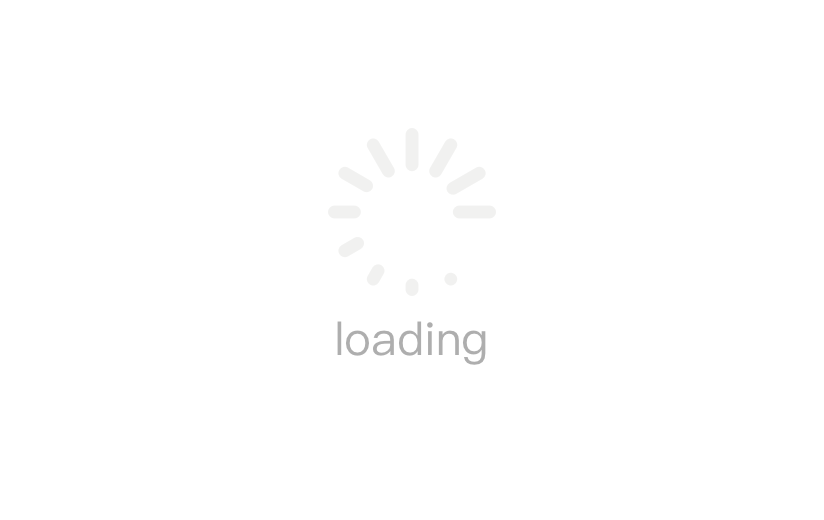