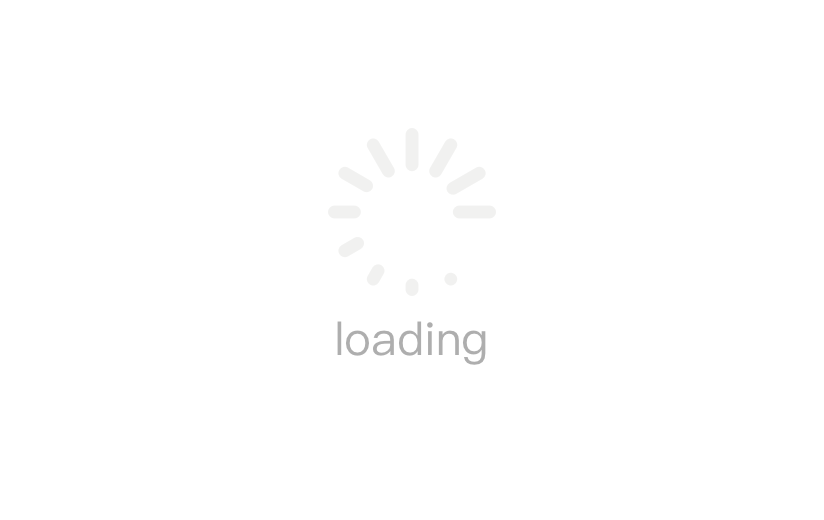
Laser cutting is almost the most advanced cutting technique in the world. It is capable of cutting both metal and non-metal materials. Whether you are in automobile industry, engineering machinery or home appliance industry, you can often see the trace of laser cutting. Laser cutting incorporates features like high precision manufacturing, high flexibility, the ability of cutting irregular shape and high efficiency. It can solve the challenges that traditional methods couldn’t solve. Today, we are going to tell you some basic knowledge of the laser cutting technology.
Working principle of laser cuttingLaser cutting is equipped with a laser generator which emits high energy laser beam. The laser beam will then be focused by the lens and form a very tiny high energy light spot. By focusing the light spot on appropriate locations, the materials will absorb the energy from the laser light and then evaporate, melt, ablate or reach the ignition point. Then the high pressure auxiliary air (CO2, Oxygen, Nitrogen) will blow away the waste residue. The laser head is driven by a servo motor which is controlled by program and it moves along the pre-determined route on the materials in order to cut out work pieces of different shapes.
Categories of laser generators (laser sources)
Light can be categorized by red light, orange light, yellow light, green light and so on. It can be absorbed or reflected by objects. Laser light is also light. And laser light with different wavelength has different features. The gain medium of the laser generator which is the medium that turns electricity into laser decides the wavelength, output power and application of the laser. And the gain medium can be gas state, liquid state and solid state.
1.The most typical gas state laser is CO2 laser;
2.The most typical solid state laser includes fiber laser, YAG laser, laser diode and ruby laser;
3.Liquid state laser uses some liquids like organic solvent as the working medium to generate laser light.
Different materials absorb laser light of different wavelengths. Therefore, laser generator must be carefully selected. For the automobile industry, the most commonly used laser is fiber laser.
The working modes of the laser sourceLaser source often has 3 working modes: continuous mode, modulation mode and pulse mode.
Under continuous mode, the output power of the laser is constant. This makes the heat which enters the materials is relatively even, so it is suitable for speed cutting. This can not only improve the working efficiency but also worsen the effect of the heat-affecting zone.
Under modulation mode, the output power of the laser equals to the function of the cutting speed. It can maintain the heat that enters the materials at relative low level by limiting the power at each spot in order to avoid the uneven cutting edge. Since its control is a little complicated, the working efficiency is not high and can only be used for a short time.
Pulse mode can be divided into normal pulse mode, super pulse mode and super-intense pulse mode. But their main differences are only the differences of intensity. Users can make a decision based on the features of the materials and the precision of the structure.
To sum up, laser often works under continuous mode. But in order to get the optimized cutting quality, for certain kinds of materials, it is necessary to adjust the feed speed, such as the speed up, speed cut and delay when turning. Therefore, under continuous mode, it is not enough just to lower the power. Laser power must be adjusted by changing the pulse.
The parameter setting laser cuttingAccording to different product requirements, it is necessary to keep adjusting the parameters under different working conditions to get the best parameters. The nominal positioning accuracy of laser cutting can be up to 0.08mm and repeated positioning accuracy can be up to 0.03mm. But in the actual situation, the minimum tolerance is like ±0.05mm for aperture and ±0.2mm for hole site.
Different materials and different thickness require different energy of melting. Therefore, the required output power of the laser is different. In the production, factory owners need to make a balance between production speed and quality and select the suitable output power and cutting speed. Therefore, the cutting area can have appropriate energy and the materials can be melted very effectively.
The efficiency that laser turns electricity into laser energy is around 30%-35%. That means with input power of around 4285W~5000W, the output power is only around 1500W. The actual input power consumption is far bigger than the nominal output power. Besides, according to the law of conservation of energy, other energy turns into heat, so it is necessary to add an
industrial water chiller.
S&A is a reliable chiller manufacturer that has 19 years of experience in laser industry. The industrial water chillers it produces are suitable for cooling a wide variety of lasers. Fiber laser, CO2 laser, UV laser, ultrafast laser, laser diode, YAG laser, to name a few. All of the S&A chillers are constructed with time-tested components to ensure trouble-free operation so that users can rest assured using them.
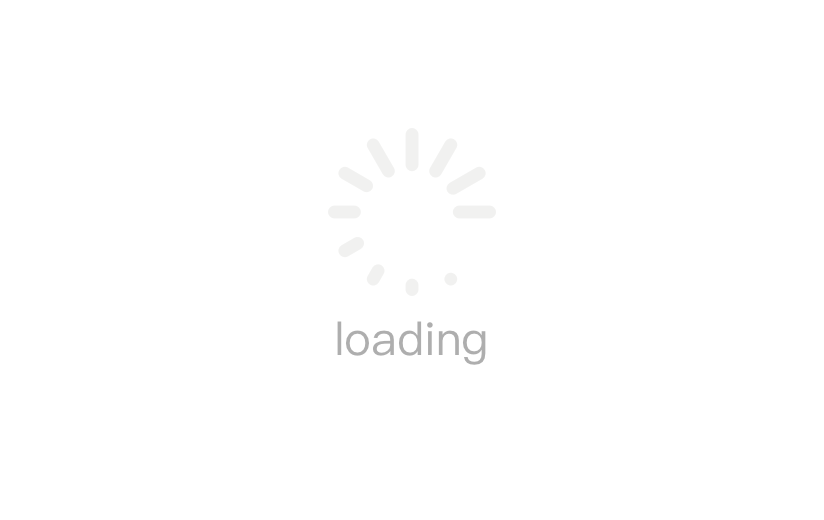